Surface Treatment
There are many types of surface treatment at On Hing Metal. After we fabricate products out of aluminum, zinc, or steel, we usually apply four main surface treatments: powder coating, paint, electroplating, and anodizes.
These treatments are either for protection from erosion or for the cosmetics effect. To prepare for the surface treatment process (P4P), a rough pre-surface treatment must be completed on the product for a smoother surface, such as polishing, sandblasting, or tumbling. This allows a smooth, seamless surface after the paint or electroplating is applied onto the surface of the product.
Sometimes there are logos and other patterns that can printed onto a surface after surface treatment. These are called transfer print and silk print.
Powder Coating
Liquid Paint Coating
Electroplating
Anodizing
Powder coating is one of the most durable finishes applied to industrial and consumer products. Powder coating offers excellent color, texture, and glossiness options, provides superior corrosion protection (up to 120 hours of salt spray test), and is safe and environmentally friendly. There are two types of powder coatings: thermoplastic and thermosetting. Thermoplastic powders melt and flow when heat is applied, but they have the same chemical composition once they cool and solidify. Thermosetting powder coatings also melt when exposed to heat, but they then chemically cross-link within themselves or with other reactive components. As a result, the cured coating has a different chemical structure than the basic resin. Thermosetting layers are heat-stable and, unlike thermoplastic powders, will not soften back to the liquid phase when reheated. Thermoset powders can also be applied by spray application to develop thinner films with a better appearance than some thermoplastic powder coatings.
Paint Coating is liquid coatings applied by spray, dip, and flow. All of these applications of liquid spray paint are Airless / air-assisted electrostatic spraying power pack that charges the atomized paint droplets. Electrostatic spraying equipment captures coating droplets as they pass or contact an electrode. It relies upon the attraction of opposite electrical charges. Dip coatings are for industrial products that only need erosion protection and do not care about aesthetics. Because dip-coating applies a layer, they often have inconsistent thicknesses, resulting in the product's measurement being altered.
Electroplating is a process where usually shiny cosmetic products. For example, fashion jewelry uses electroplating gold or rhodium, automobile parts use chrome electroplating, and some non-kitchen appliances use shiny metal electroplating. Electroplating should not be confused with E-coat because E-coat is a thin layer of clear organic coating. Electroless Nickel plating can be just for protection. However, the utility of electroplating is that the product can still be electrically conductive after the surface treatment protection.
The surface treatments explained above to add an extra layer on top of the product. However, it is very different from anodizing an aluminum part; anodizing causes the outside natural oxide layer to become thicker, leading to better corrosion and wear resistance. The product may decrease smaller in size during this process, and colours can be mixed into the anodizing treatment.
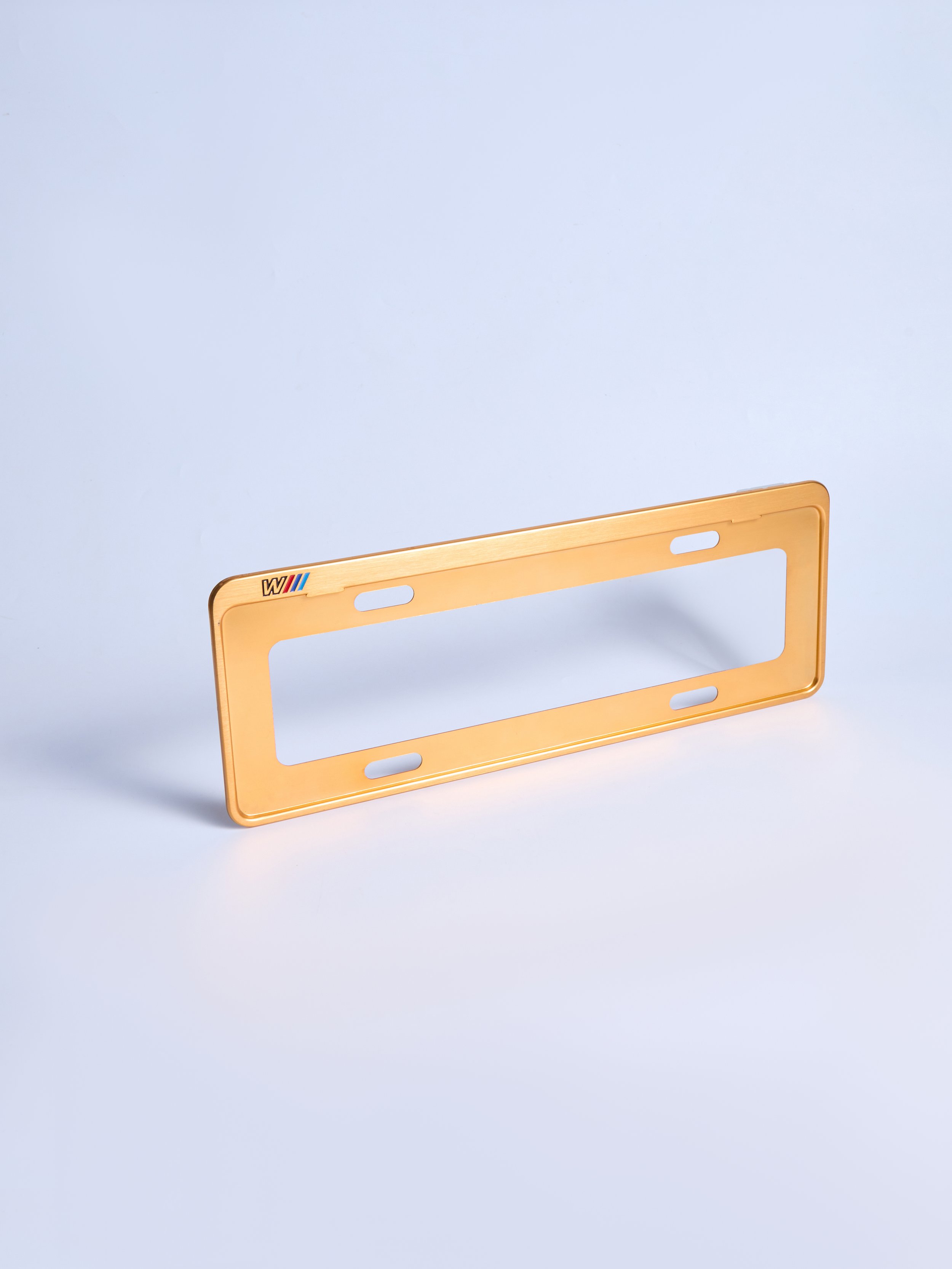
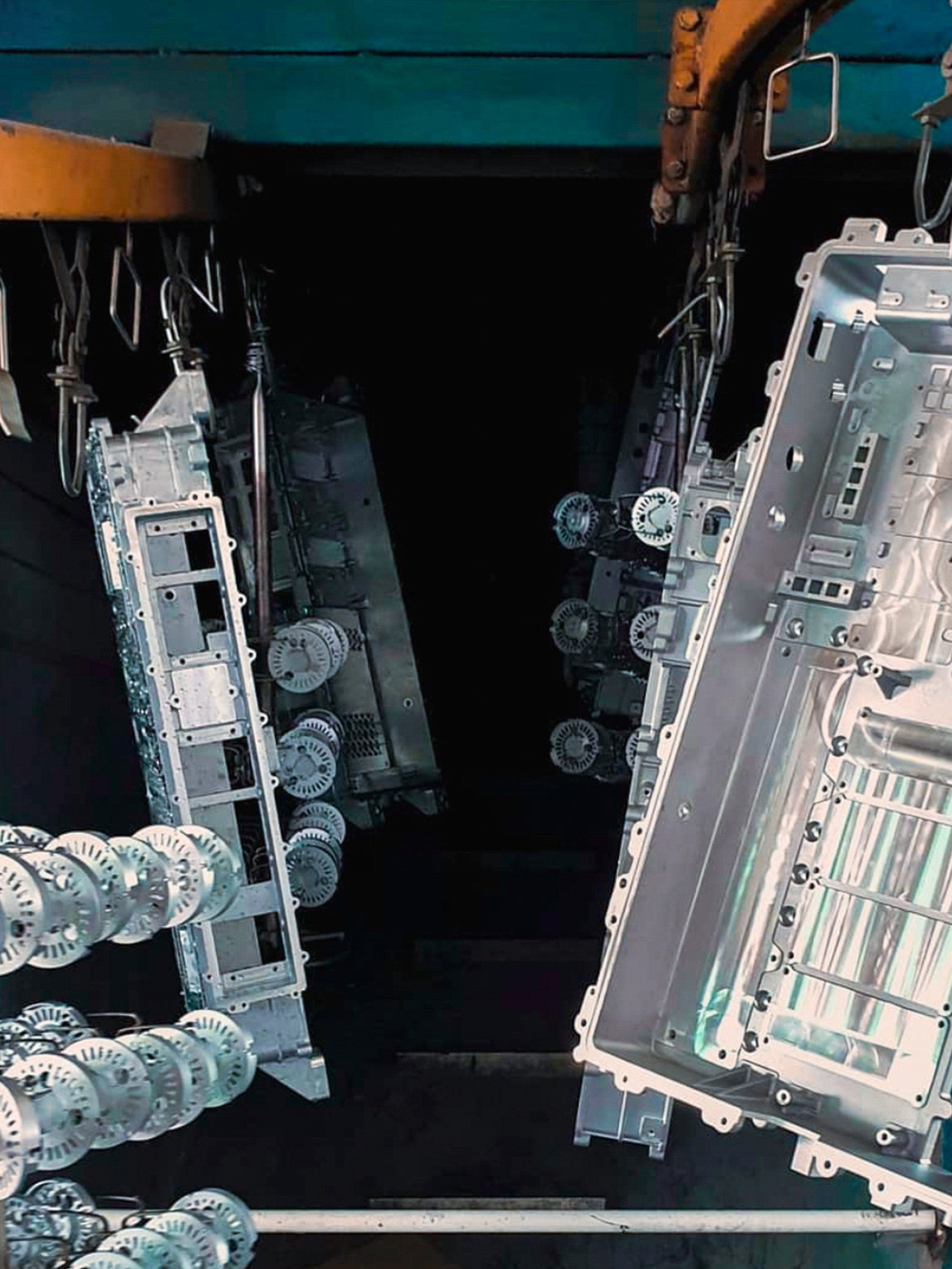
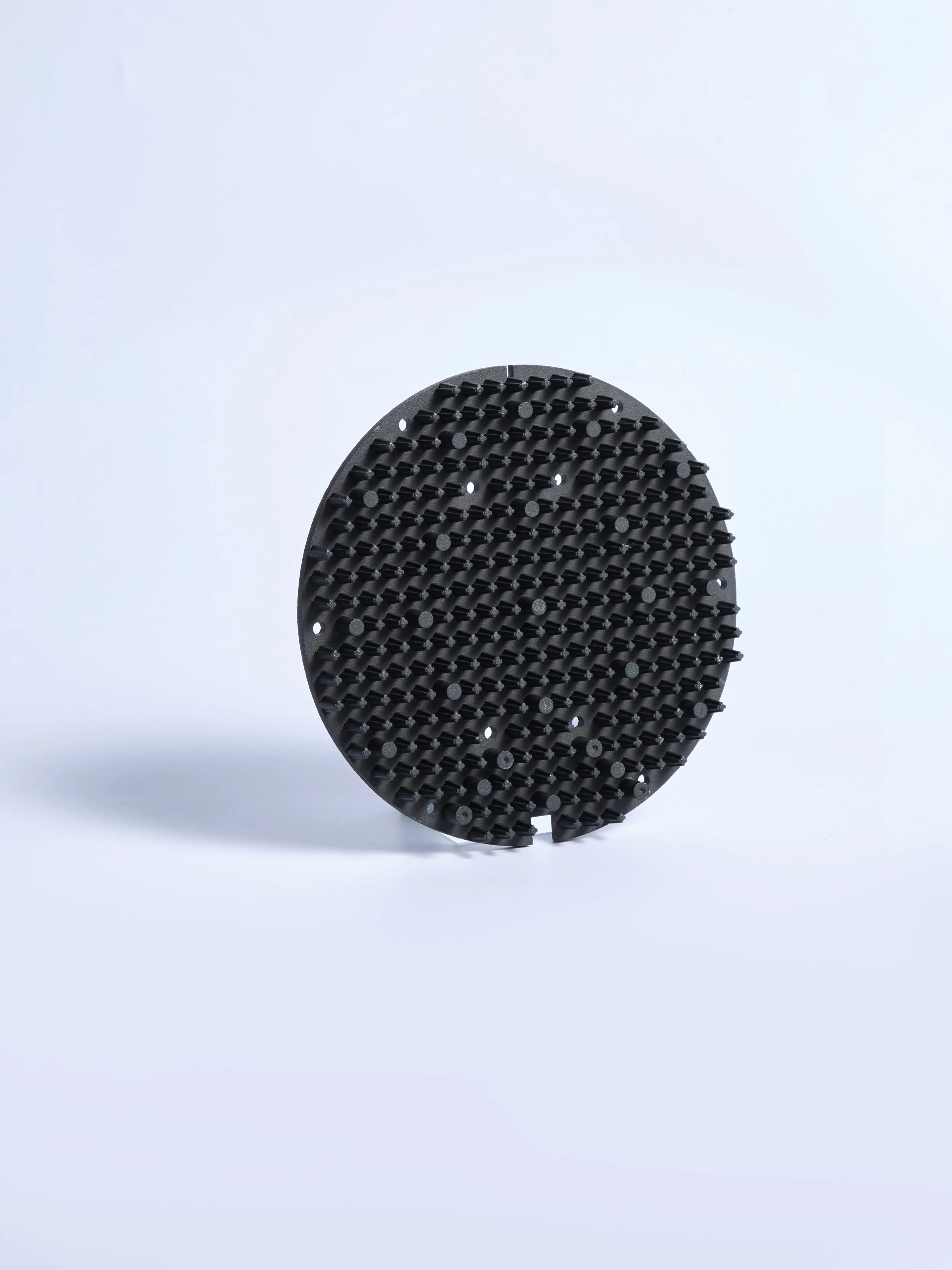
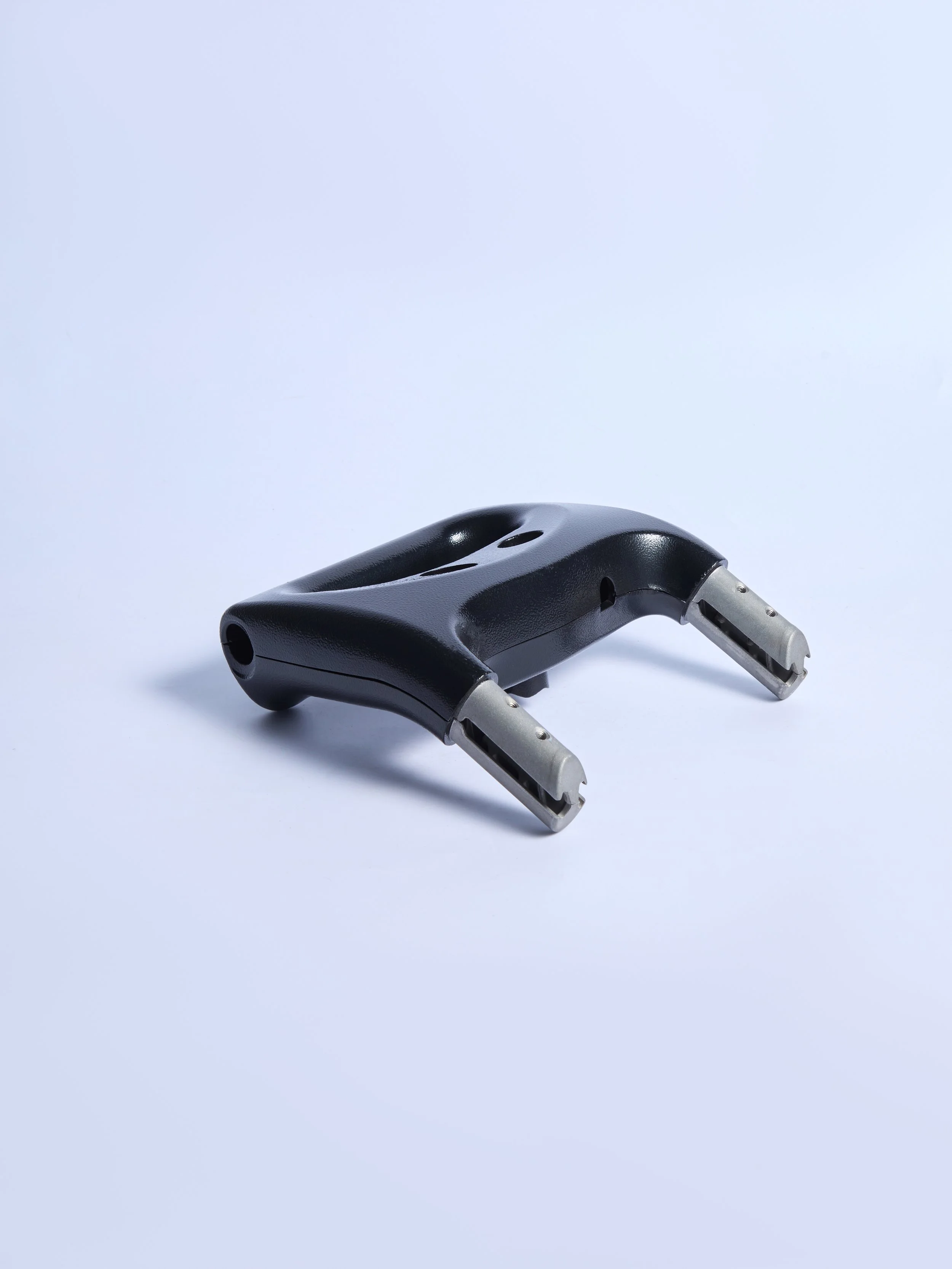
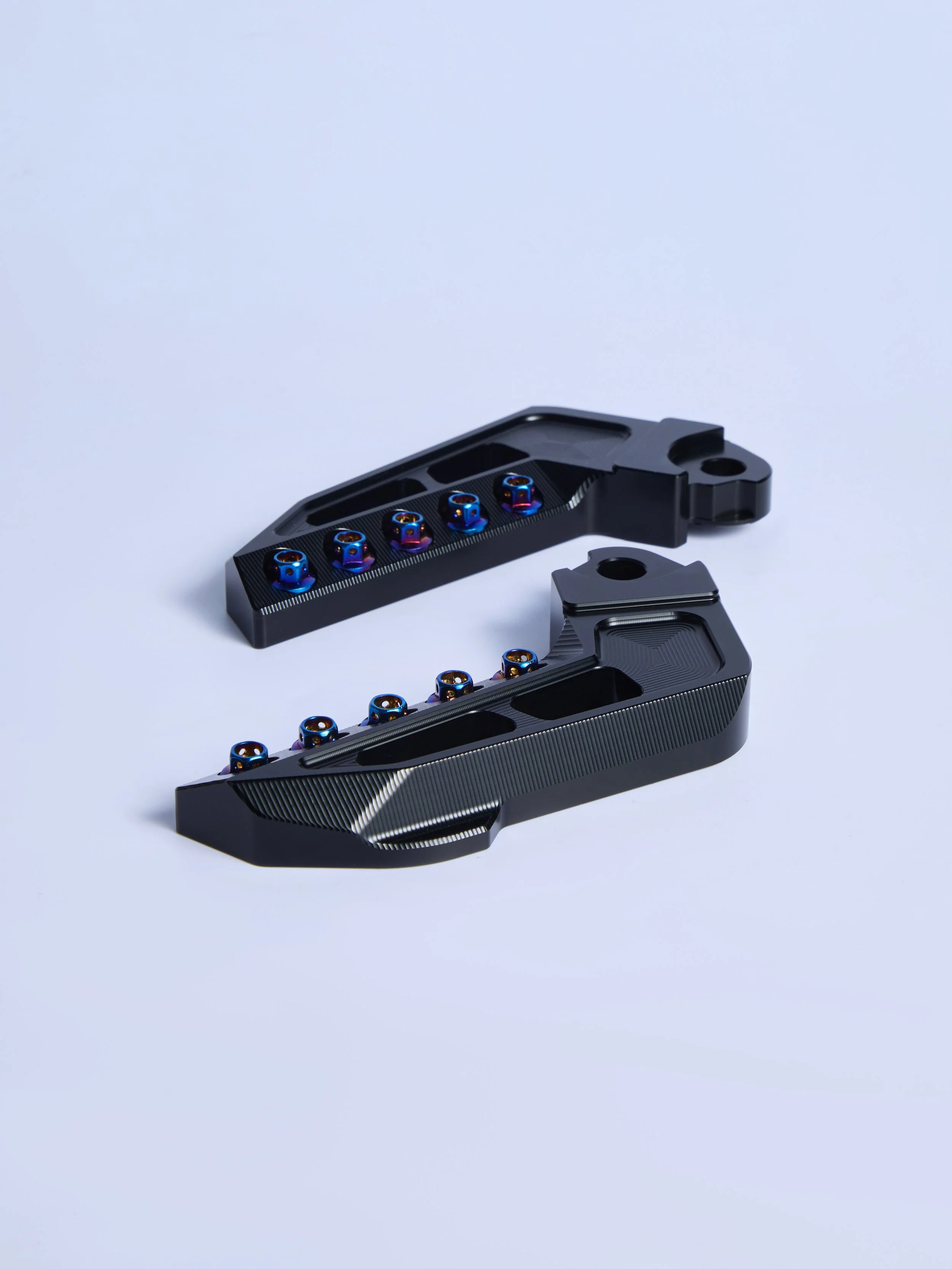
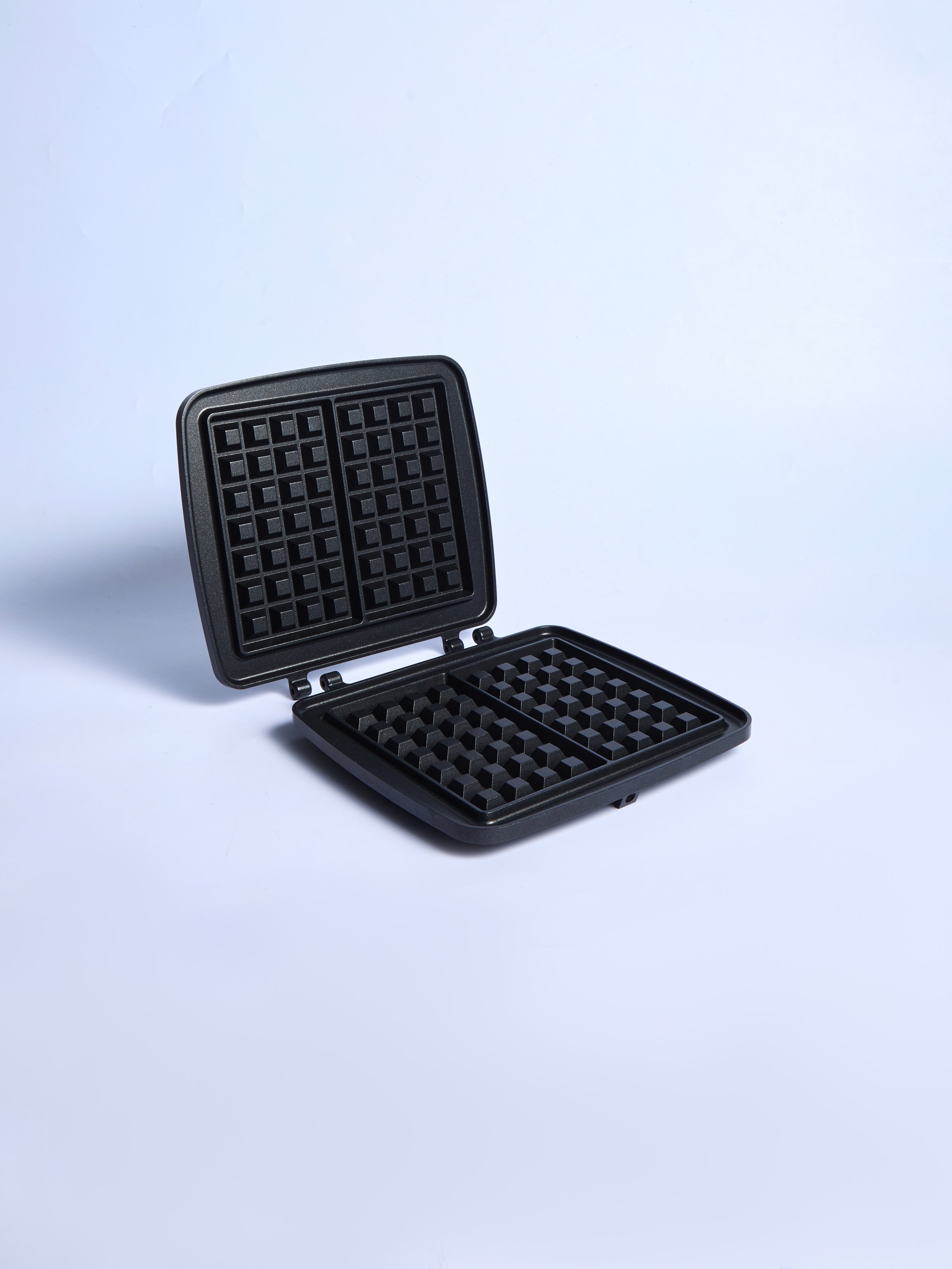
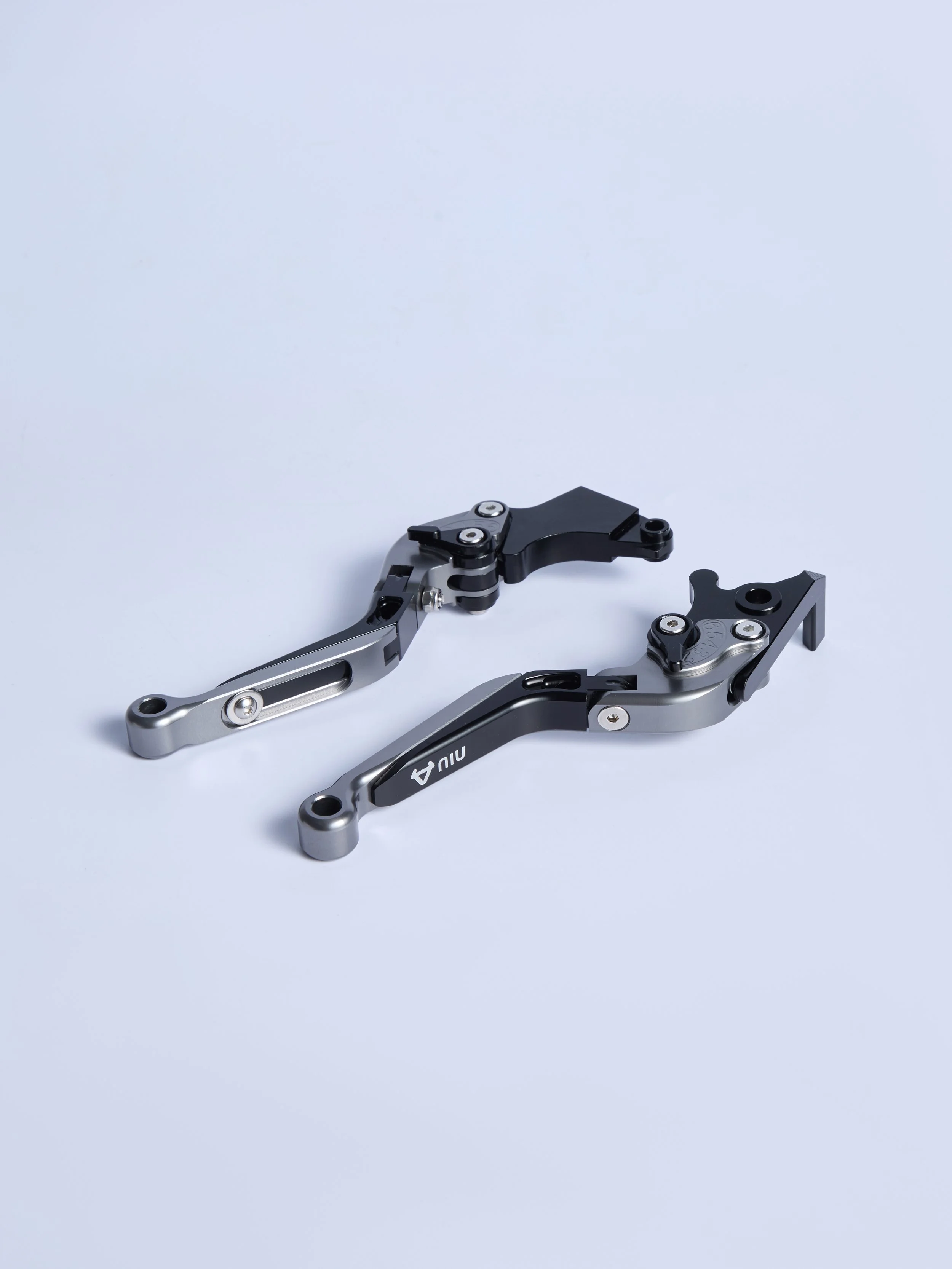
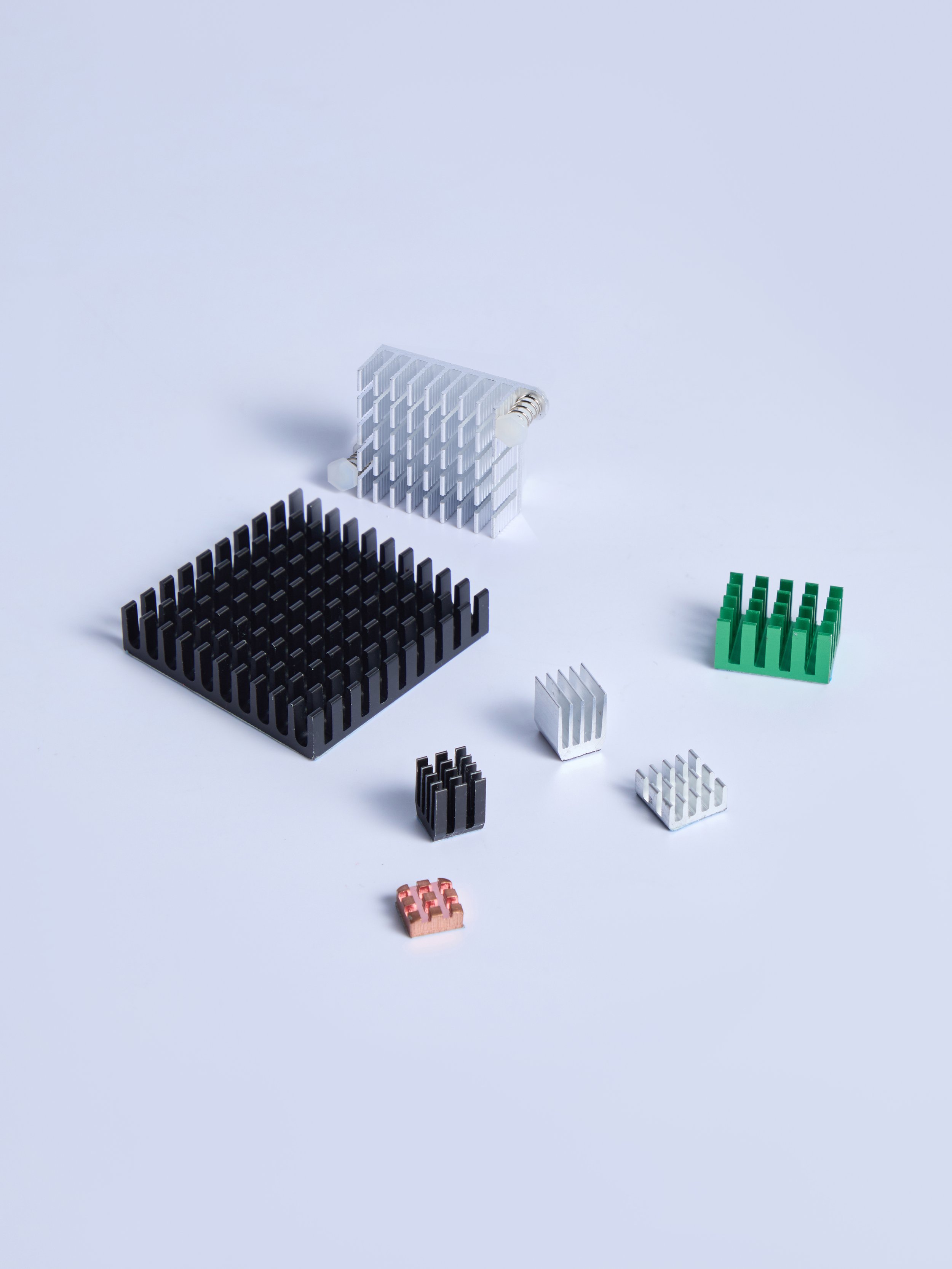



